
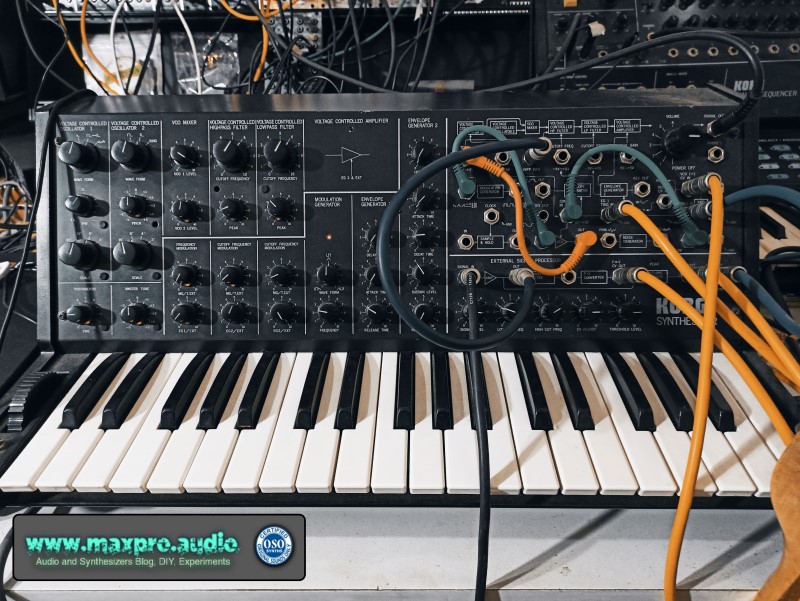
My poor synth was diagnosed as dead and no longer “resurrectable” (yes, resurrection is not that uncommon with electronic equipment), several years ago, already.
On the last visit by my former audio technician, the response was:
“Buy yourself a new Behringer clone, they’re not too expensive ..”
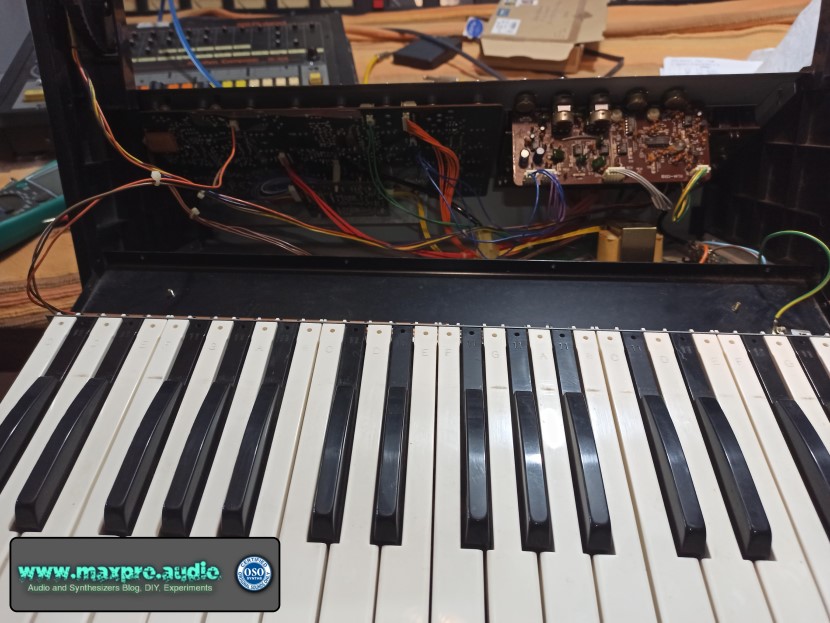
No, I couldn’t accept that my first synth was destined to be thrown away! Apart the economic side, there is another aspect that always makes me think: The old keyboards are a piece of our history, witnesses of our technological evolution and often rare survivors of other times, but not for these reasons, musically outdated. Indeed, like important art objects, they should be protected by special laws! :D
OK, joking aside, on those times, my technical knowledge in electronics was not sufficient to being able to make a diagnosis and schematics, looked to me like hieroglyphs of some alien race.
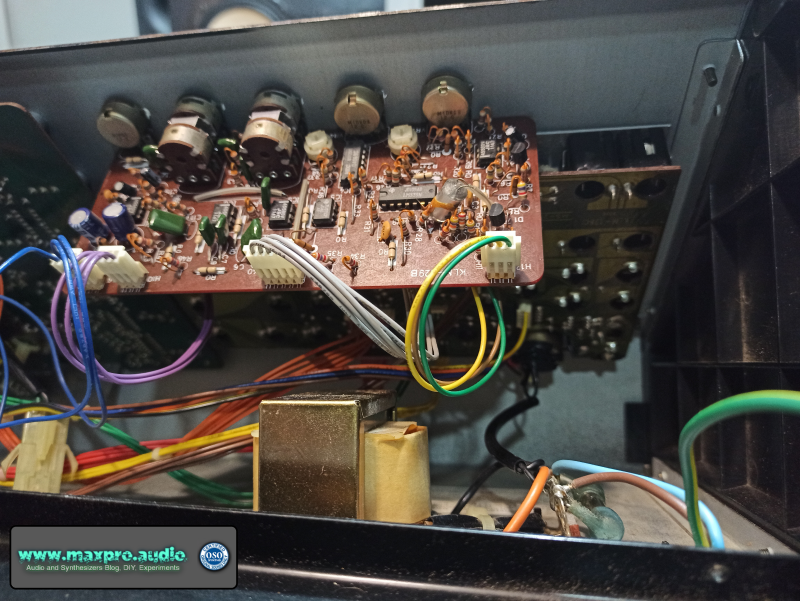
But with patience, reading texts, watching videos and consulting friends, I started to become more aware on how my old and stinky electronic musical instruments work, even inside their panels.
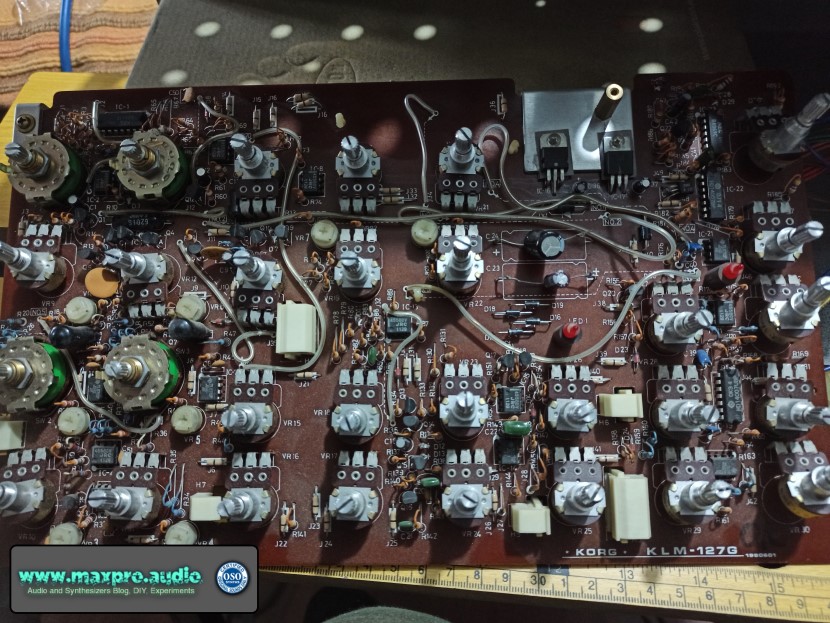
My synth remained open in a corner of the studio for very long, I walked past it without even seeing it, almost to avoid the pain of having to give up, but one day everything changed: I looked at it carefully and whispered “don’t worry my friend, we’ll be back playing together, like in the old days, very soon!” … Well, to tell you the truth, it wasn’t very soon really, but the promise was becoming true. The KORG MS-20 started always being on my mind and I was looking for information and literature to prepare myself to the repair.
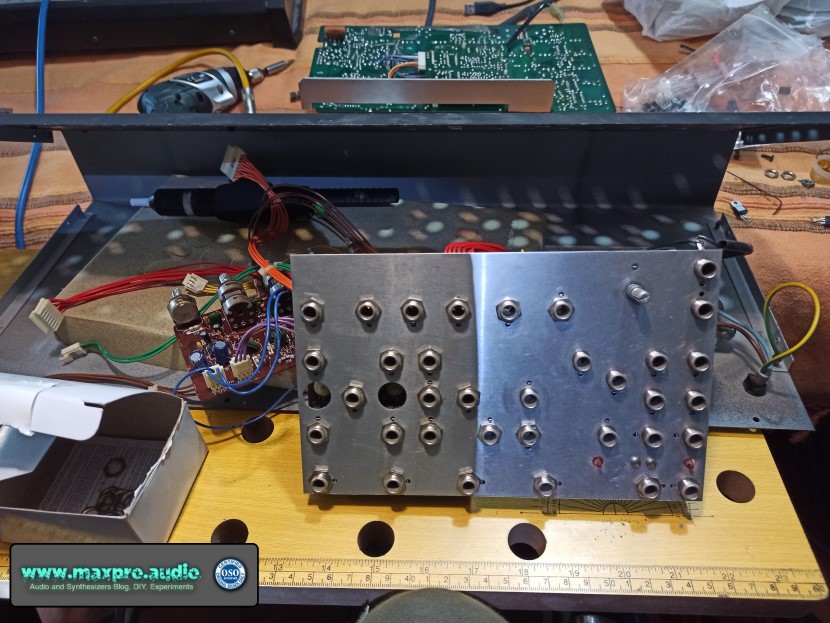
It took a couple of weeks to “unravel the problem”, check what the hell was wrong with it and try to figure out why the previous attempts had failed.
Lacking power to one of the rails, I imagined there was a problem in the power source, but the fact that the technician hadn’t success, made me waste lots of time “looking” around. Eventually, to my horror, I discovered that the culprit for the inability to repair the synth was the technical manual, which unexpectedly contained an error!
Yes, I understand that it seems impossible, but it is like this: The “sacred text”, obligated reading and time saver of every technician, seems like impossible it has not been studied in detail and made “perfect” … I could not believe my eyes!
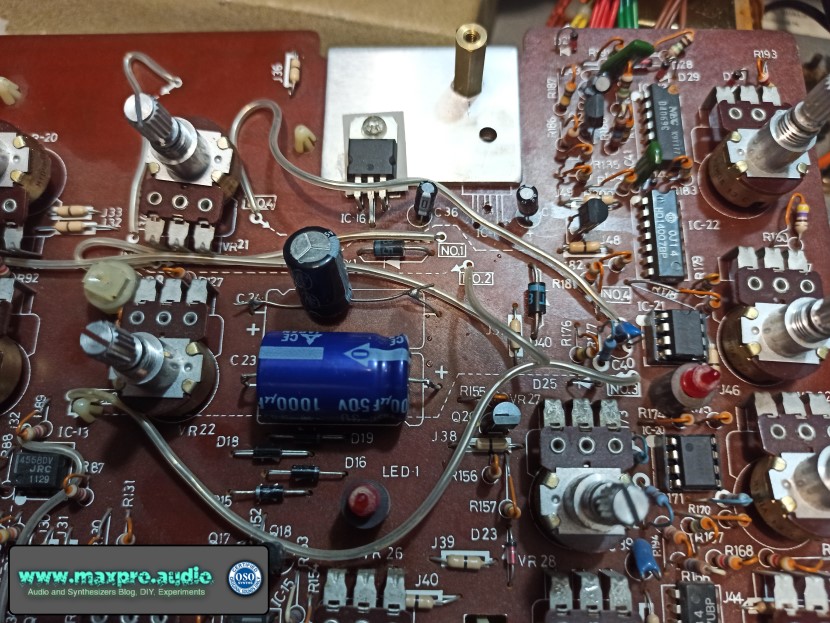
The reason is that, the only technical manual available on the internet about the synth KORG MS-20, it had a strange “BAD COPY” stamped on the cover, but having been misprinted, I thought the warning was related to this aspect. Who would have thought that BAD was SO BAD! : D
Usually, a technical manual has a “layout” with the graphics of the components mounted on the board, with their relative values, a list of the installed components and the technical diagrams with the paths of the tracks and the symbol of the components. In this case, in the layout, the two voltage regulators were reversed and without a thorough study of the scheme, comparing the tracks with the real ones, the diagnosis would have been that of my technician, “non-repairable synth“.
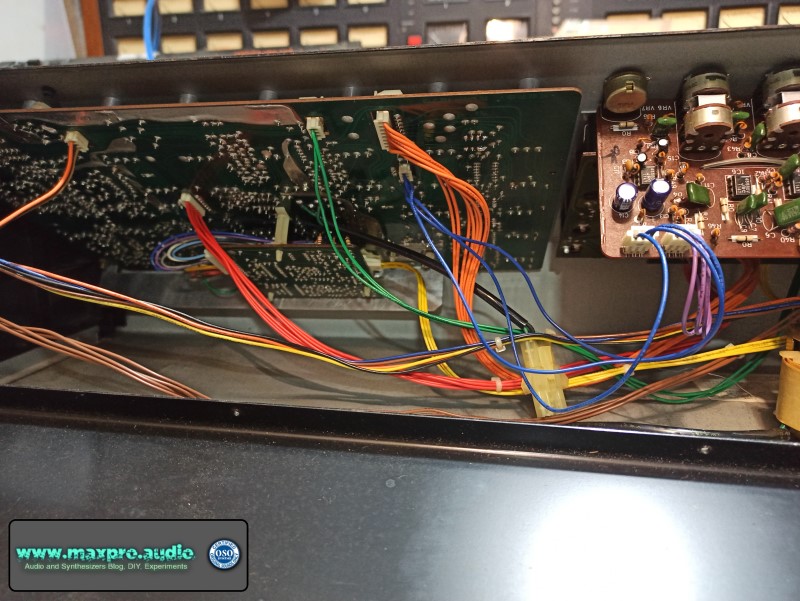
Once the trick was discovered, it took a few minutes to “resurrect” the synth. You cannot imagine the happiness of seeing the mini-LED of the LFO flash again, to remain still in a metaphysical environment, “after the long death!”
(2021 Massimo Belladonna – maxpro.audio)